Do You Know Why Aluminum Framing is the Gold Standard for Machine Guarding Safety?
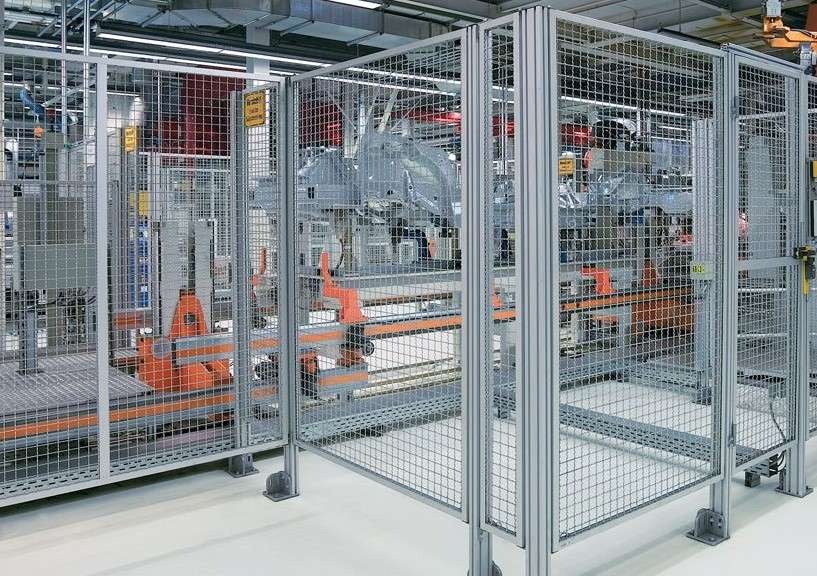
Industrial workplaces demand strong and reliable safety measures to protect workers and equipment. Machine guarding is a key component of workplace safety, and aluminum framing has become the preferred choice for creating durable, adaptable, and effective barriers. Here’s why aluminum framing leads the way in machine guarding solutions.
Impact Resistance That Shields Workers from Hazards
Heavy machinery poses significant risks, and weak barriers won’t cut it when protecting workers from moving parts, flying debris, or accidental collisions. Aluminum framing is engineered for impact resistance, absorbing force without bending or breaking. Unlike traditional steel barriers that dent under repeated stress or plastic guards that crack over time, aluminum maintains its structure while remaining lightweight.
In manufacturing plants and automation facilities, machine guarding must withstand constant use. Forklifts, conveyor belts, and robotic arms operate with force, making strong enclosures necessary. Aluminum framing creates rigid structures that can absorb impacts while keeping workers safe. The material’s durability ensures a longer lifespan, reducing maintenance and replacement costs compared to weaker alternatives.
Non-Sparking Properties for High-Risk Work Environments
Industries dealing with flammable materials, such as chemical processing, oil refineries, and aerospace manufacturing, require non-sparking safety solutions. Aluminum framing naturally resists sparking, making it a safer alternative to steel in hazardous work areas. When metal tools or machinery components come into contact with aluminum, there’s no risk of sparks igniting combustible dust or gases.
This safety advantage is critical in environments where traditional steel guards pose a fire hazard. Additionally, aluminum framing resists corrosion, ensuring long-term reliability even in harsh conditions. Unlike iron-based metals that rust over time, aluminum remains intact, maintaining its safety properties without costly treatments or coatings.
High-Visibility Options for Clear Safety Zones and Barrier Markings
Machine guarding isn’t just about physical barriers—it’s also about visibility. Workers must be able to see safety zones clearly, and aluminum framing allows for bright, highly visible configurations. Many systems include powder-coated finishes or anodized colors to enhance visibility, ensuring barriers stand out in busy industrial environments.
In factories and warehouses, color-coded machine guards improve safety by designating restricted zones, emergency exits, or high-risk areas. Aluminum framing integrates easily with acrylic panels, mesh, or polycarbonate shields, enhancing protection while maintaining a clear line of sight to machinery. This prevents accidental entry into dangerous areas and helps workers stay aware of their surroundings.
Precision Engineering That Eliminates Gaps and Weak Spots
Gaps in machine guarding create risks, allowing debris or body parts to slip through unsafe openings. Poorly designed barriers can leave workers exposed to hazards, defeating the purpose of protective enclosures. Aluminum framing provides precise, modular construction that eliminates weak spots while allowing full customization for different applications.
Manufacturers benefit from aluminum’s flexibility, which enables machine guarding to fit snugly around equipment without unnecessary gaps. Unlike welded steel structures that require labor-intensive modifications, aluminum framing is adjustable, allowing for quick reconfigurations as production layouts change. This adaptability ensures complete coverage without compromising access to machinery for maintenance.
Compatibility with Sensors and Automation for Enhanced Protection
Modern industrial safety systems rely on automation, and aluminum framing is fully compatible with sensors, interlocks, and electronic safety controls. Unlike traditional barriers that simply block access, aluminum-framed machine guards integrate seamlessly with smart safety features. Motion detectors, light curtains, and automatic shutdown systems can be mounted directly onto the frame, creating a responsive safety network.
In high-tech manufacturing, this integration prevents unauthorized access while allowing for real-time hazard detection. The lightweight structure of aluminum framing makes it easier to install wiring and mounting brackets without compromising strength. As automation becomes more prevalent in workplace safety, aluminum framing continues to be the preferred choice for machine guarding solutions.
Cost-Effective Safety Solutions Without Compromising Strength
Safety should never be compromised by budget constraints, and aluminum framing provides an affordable yet highly durable alternative to steel or custom-built enclosures. Traditional machine guarding materials often require expensive welding, additional coatings for corrosion resistance, and heavy-duty support structures. Aluminum framing eliminates these extra costs while delivering superior performance.
Installation is faster and easier with aluminum, reducing labor costs and minimizing downtime in industrial operations. Additionally, the long lifespan of aluminum reduces replacement expenses over time. Its lightweight nature lowers transportation and handling costs, making it a cost-effective investment for facilities looking to improve safety without exceeding their budget.