Types of Maintenance Services Offered by Control System Integrators Post-Project Completion
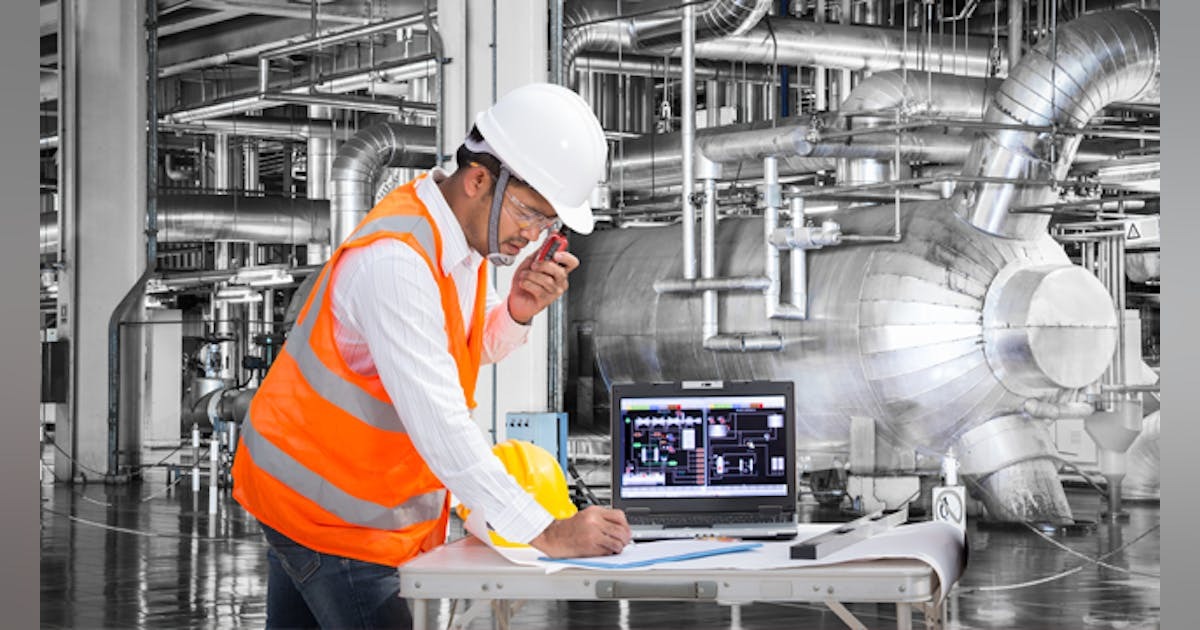
Once a control system is up and running, the work doesn’t stop there. Ensuring it operates smoothly over time is essential for keeping a facility efficient and productive. That’s where control system integrators come in with their range of post-project maintenance services. These services are designed to prevent downtime, resolve issues, and keep everything running optimally. Let’s take a closer look at the types of maintenance services you can expect from a control system integrator.
Preventative Maintenance to Avoid System Downtime
Preventative maintenance is all about catching potential problems before they become real issues. Control system integrators offer regular checks and maintenance tasks designed to keep systems in peak condition. By addressing wear and tear early, companies can avoid the costly downtime that often comes with unexpected breakdowns. This approach helps minimize disruptions and keeps everything running as smoothly as possible.
A preventative maintenance plan typically includes scheduled inspections, performance testing, and part replacements. A control system integrator will ensure all components are operating correctly, checking for any signs of stress or failure. By sticking to a regular schedule, the risk of major system failures is reduced, helping facilities avoid unnecessary repairs or expensive emergency services.
Corrective Adjustments for Immediate Issue Resolution
Even with the best preventative maintenance, problems can still arise. That’s where corrective adjustments come into play. When issues occur, control system integrators are on hand to make the necessary fixes quickly. Corrective maintenance focuses on identifying the root cause of a problem and implementing solutions immediately to get the system back up and running.
Whether it’s a hardware malfunction or software glitch, a control integrator can diagnose the issue and resolve it efficiently. Their expertise allows them to troubleshoot quickly, minimizing downtime and restoring system performance. Immediate issue resolution is critical for businesses that rely on continuous operation, and having a trusted control system integrator ensures that issues are resolved with minimal impact on productivity.
Software Updates and Patches for Optimal Performance
As technology evolves, so do the systems that run it. To keep control systems running optimally, software updates and patches are essential. A control system integrator regularly provides updates that enhance functionality, fix bugs, and improve security. Without these updates, systems can become outdated and vulnerable to potential threats.
Software maintenance is often overlooked, but it’s crucial for long-term performance. Control integrators ensure that updates are tested and applied without causing interruptions to ongoing operations. Patches can resolve minor issues, while major updates can introduce new features and enhance the overall efficiency of the system. Regular software maintenance keeps systems current and protected from evolving risks.
System Calibration to Maintain Operational Accuracy
Calibration is a vital maintenance service that ensures the accuracy of control systems. Over time, sensors and other system components may drift from their original settings, which can affect the system’s performance. Regular calibration is necessary to maintain the precision and reliability of the system, especially in industries that depend on high accuracy for their operations.
Control system integrators are responsible for calibrating equipment to ensure it’s functioning at the right specifications. This process involves adjusting sensors, controllers, and other elements to bring them back into alignment with the desired performance standards. Without regular calibration, systems can become less efficient, leading to errors and decreased productivity. Control system integrators provide the expertise needed to keep everything finely tuned and working as expected.
Remote Diagnostics for Swift Troubleshooting
Remote diagnostics is a powerful tool that allows control system integrators to troubleshoot issues without having to be physically present on-site. Using advanced monitoring tools, they can detect problems in real-time and often resolve them remotely. This service can significantly reduce response times, allowing for quicker fixes when issues arise.
Remote diagnostics not only saves time but also helps prevent minor issues from escalating into major problems. By monitoring system performance continuously, control system integrators can identify and address abnormalities before they affect operations. This proactive approach ensures that businesses experience less downtime and fewer disruptions in their daily processes.
On-Site Support for Complex Hardware Repairs
While many issues can be resolved remotely, some problems require hands-on attention. For complex hardware repairs, on-site support is essential. Control system integrators offer skilled technicians who can visit your facility, diagnose hardware issues, and perform necessary repairs or replacements.
On-site support is particularly important for large-scale or intricate systems where specialized tools and knowledge are required. Whether it’s replacing a faulty component or recalibrating equipment after a repair, control system integrators ensure that your system is restored to full functionality. Their ability to provide on-site expertise when needed is crucial for minimizing downtime and maintaining the performance of critical systems.