How to Test and Validate a Pipeline Leak Detection System
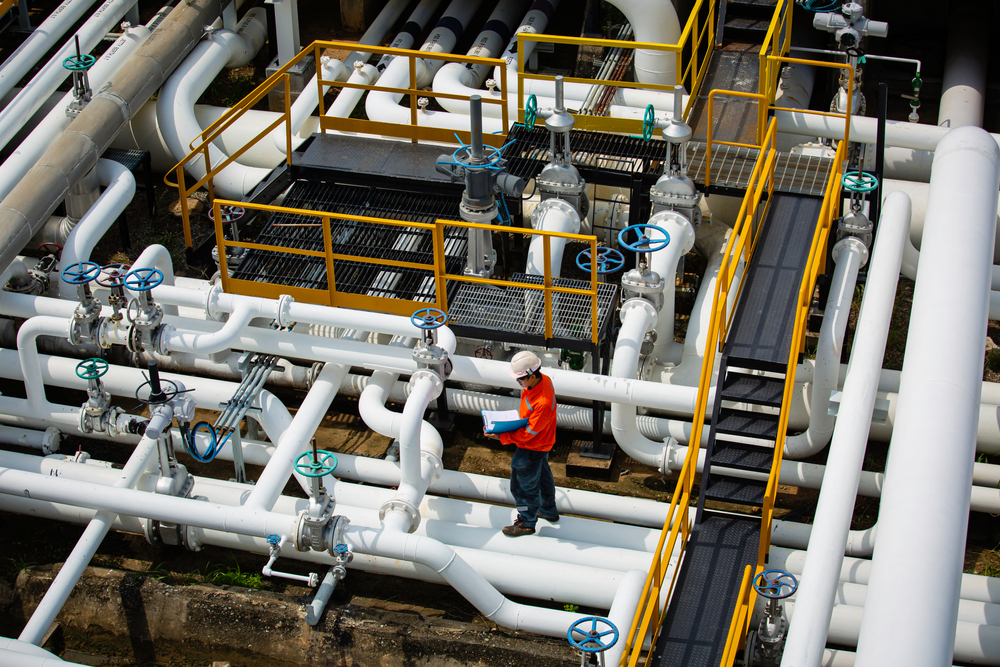
All around the world, there are numerous networks of pipelines transporting different types of materials. These varied materials range from oil and natural gas to fiber optics carrying crucial data. The transportation of these materials through the pipelines can be within the country, from one country to another, or even from one continent to another. With such a vast network of pipelines carrying hazardous materials, it needs constant monitoring, testing, and maintenance for safe transportation. To ensure that this takes place proficiently, it is vital for companies that take care of these pipelines to implement a robust pipeline leak detection system.
What is a Pipeline Leak Detection System?
There are hazardous pipeline transportation systems around the globe, and each of these systems has a risk connected with its use. Therefore, leak detection is a crucial component of ensuring the prevention of such leaks. It gives early notice of a potentially significant occurrence, allowing for a quicker reaction to pipeline leakages.
Testing and Validating a Pipeline Leak Detection System
To test and validate a leak detection system which is a complex procedure, pipeline companies often deploy various technologies and methods as given below:
1) Computational Pipeline Monitoring:
Computational Pipeline Monitoring (CPM) systems are the most often used approach for oil and gas pipeline leak detection. This technique claims that the difference between the mass flow rates into and out of a pipeline segment must match the rate of mass accumulation, commonly known as the packing rate, in that pipeline section. It does this by using the idea of conservation of mass. In mass balance, a leak would manifest as a disparity referred to as a leak signal. CPM is an established technique that is reasonably trustworthy.
2) Real-Time Transient Model:
RTTM Real-Time Transient Model employs mathematical models based on physical principles to locate pipeline breaches. Since they utilize mass, momentum, and energy conservation, RTTM approaches are advanced over balancing techniques. In real-time, the method determines mass flow, pressure, density, and temperature at many pipeline points. Gas pipelines can detect steady-state and transient leaks using this technology. Modern RTTM-based pipeline flow systems use intake and exit pressure and temperature. The projected flow is compared with input and outflow meters. Then estimated and observed input or output quantities are measured to check the flow difference. Leaks modify the pressure and calculated flow while observed flow remains unchanged and is a more transparent and precise signal. RTTM simulates pipeline conditions using fluid mechanics and hydraulics.
3) Pressure Point Analysis:
Pressure point analysis is a method for testing and validating pipeline leak detection by analyzing pressure or velocity pipeline readings at a single place before and after a breach. A leak modifies the pipeline’s hydraulics, affecting pressure and flow. The approach identifies leaks by measuring pipeline pressure at a particular moment and comparing it to a running statistical trend. The leak’s pressure wave source extends upstream and downstream. The leak’s wave is a negative pressure wave, with the pressure before the leak serving as a reference. The intake and output pressures drop when the negative pressure wave reaches the pipeline terminal. The determination of a leak spot happens based on pressure difference, pipeline length, and negative pressure wave velocity. Pressure point analysis may find leaks other techniques miss.
4) Magnetic Induction Procedure:
Magnetic Induction (MI) uses internal and exterior sensors. Inside sensors monitor pressure, fluid velocity, and acoustic leakage vibrations; external sensors assess soil temperature, humidity, and characteristics. Outside sensors allow granular leak detection and localization. A pipeline-mounted wire coil produces magnetic induction communication, and magnetic induction transceivers connect pipeline sensors to underground sensors.
Sinusoidal current modulates the transmitter coil signal, producing a time-varying magnetic field around the transmitter and the receiver, allowing communication. MI systems enable precise real-time leakage detection and localization in severe subterranean conditions but need many sensors, resulting in high installation costs.
Also Read: Data Centralization On A Single Platform For Pipeline Leak Detection Systems
Conclusion
Pipeline leak detection system and localization of the problem in pipeline networks is a difficult study that requires thorough testing and validation. Testing evaluates how a system may function, how it now functions, tools for identifying strange events, and a method for training and assessing operators. Knowing how well things should work and how well they already function is integral to safety monitoring. In addition, before installing leak detection systems, performing an environmental evaluation to identify whether environmental factors such as air, land, water and energy may compromise the system’s operation is essential.